Tubing Burst Pressure
Tubing Burst Pressure
Randolph Austin peristaltic pumps offer the unique ability to transfer materials without coming in contact with the pump. In a sense, the tubing is the heart of the pump. Using the wrong tubing for an application and you may have a ruptured line with a mess to clean up; selecting the right tubing for the job, results in a better experience. Of the many factors to consider in any application of tubing, one is the pressure that the system is designed for. To help our customers determine the best tubing for a specific job, Randolph Austin Company designed a test that closely paralleled the specifications for burst pressure as described in ASTM 1599-99
Taking a standard length of tubing, the tubing was pressurized with inert oil until the it underwent plastic deformation. The materials we tested were Cilran™, Prothane™, ED-Plex™, and Vytex™. Each size and material combination was tested five times to establish a statistically sound average and reported in the chart below.
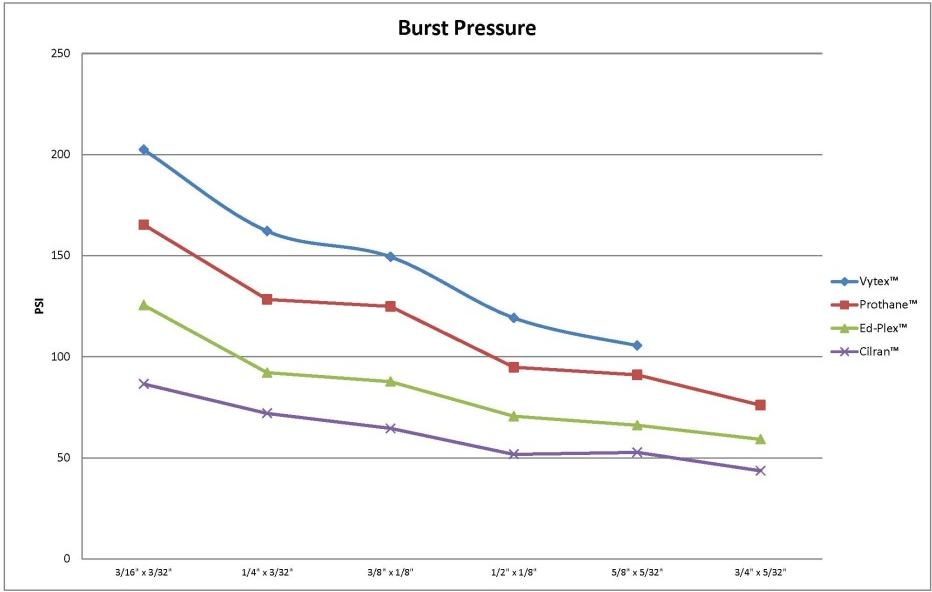
Burst Pressure
There are correlations between tensile properties, wall thickness, and inside diameter to the burst pressure of the tubing. As the inside diameter of the tubing increases so does the surface area the fluid can push against. The less area to push against, the less total force is being applied to the internal diameter of the tubing. This is why small diameter tubing can carry pressures far greater than tubing with a larger diameter.
The greater the wall thickness is, for tubing of the same internal diameter and material, the greater the resistance to pressure. The same rule applies for the tensile properties. The higher the tensile of the elastomer, the greater the burst pressure rating for that tubing made from that material. That is why for applications requiring pressure resistance we generally recommend tubing with the smallest internal diameter, the largest wall available, and the highest tensile.
In choosing the best tubing for a specific application it is important to consider other factors that adversely affect tubing performance such as temperature, operating conditions, chemical resistance and maintenance to the tubing.
Generally, increases in temperature will reduce the tensile properties of elastomeric compounds and lower their yield strength and hardness. Conversely, lower temperatures may increase yield and tensile strength a little, but they may also have a detrimental effect on the resilience of the tubing, especially as it approaches the low temperature rating for the elastomeric material. Therefore, especially for peristaltic pumps, it is important to consider the operating temperature range for any given system.
This consideration should also include a review of the chemistry of the materials being transferred, as many materials become more corrosive at higher temperatures.
Finally, but of great importance, is the chemical resistance of the tubing in the presence of aggressive fluids. Typically we see two types of failure. Some fluids will soften the tubing material by actually entering the material matrix. Usually there is swelling and loss of tensile properties under this type of chemical attack. Another common form of failure is seen when fluids leach out plasticizers used to help make the tubing flexible. This type of attack usually leads to an embattlement and early fatigue failure. Regardless of the method, when a system application is being evaluated, chemistry, pressure, temperature and the operating conditions of the pump need to be considered. The working pressure graph is intended as a guide for selecting tubing for a given application. A safety factor of three was used for establishing the values on the chart below. These are guidelines only, and not intended to replace the due diligence necessary to establish the proper operating parameters for a pump and tubing in any given application.
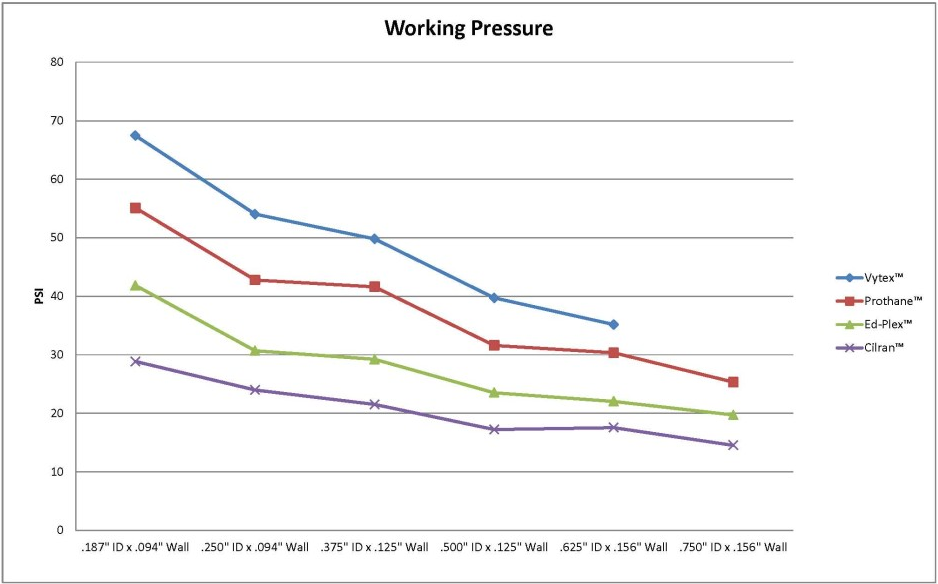
Working Pressure
Randolph Austin Company extrudes and stocks tubing sizes for peristaltic pump applications. For pricing and delivery, or specific application, questions please don’t hesitate to contact us.
Cilran™, Prothane™, ED-Plex™, and Vytex™ are the trademarks of Randolph Austin Company – Manchaca, TX
ASTM International, P.O. Box C700, West Conshohocken, PA 19428